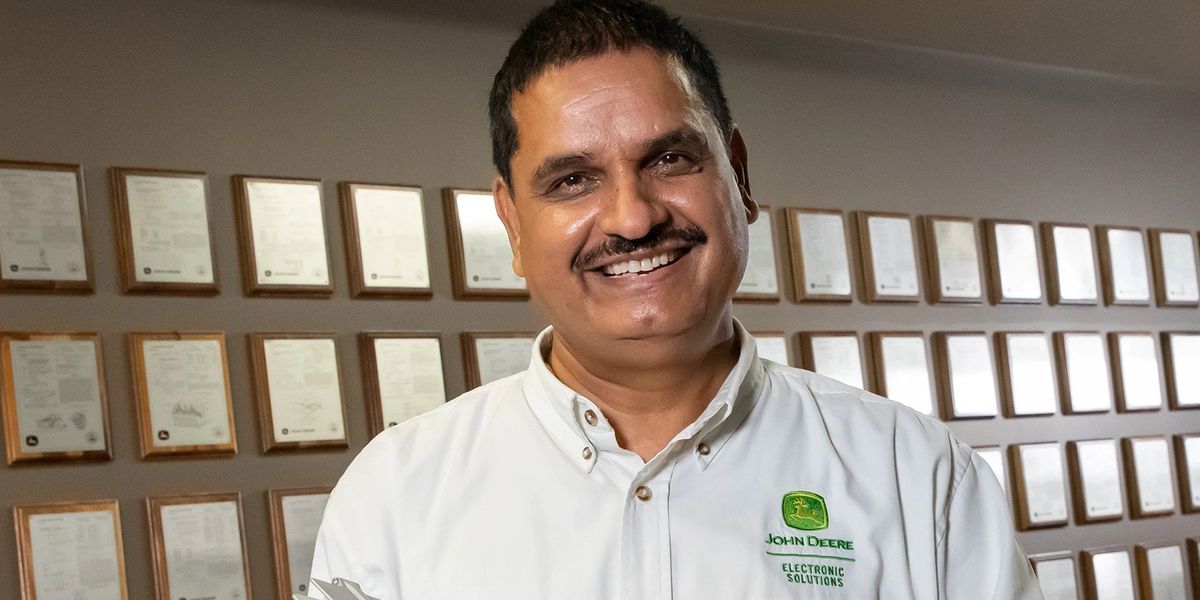

For Brij Singh, electrifying John Deere’s heavy-duty vehicles reflects his past. Singh grew up on a farm in India, and is committed to bettering agriculture’s future. John Deere, headquartered in Moline, Ill., is a leader in agricultural, construction, forestry, and turf-care machinery. Singh, a power-electronics engineer, has been working to replace the internal combustion engines used in the company’s equipment with hybrid (diesel-electric) and all-electric versions.
“Power electronics and electrification of agricultural equipment can help change our world for the better by reducing the equipment’s greenhouse gas footprint, providing food and fiber to feed, house, and clothe the world, and helping farmers stay profitable,” Singh says.
Singh grew up on a 10-hectare farm his family has owned for more than six centuries in Shahpur Charki, a 560-person village in the state of Uttar Pradesh, India.
Brij Singh
Employer:
John Deere, Fargo, N.D.
Title:
External relationships manager for Australia, Canada, New Zealand, and the United States
Education:
Bachelor’s degree in electrical engineering, Mohan Malaviya Engineering College; master’s degree in engineering, Indian Institute of Technology Roorkee; Ph.D. in engineering, Indian Institute of Technology Delhi
“I come from a long line of farmers. I personally know how important [farming] is,” he says.
In 2007, he joined John Deere’s electronics-solutions group, in Fargo, N.D., as a staff engineer. Three years ago, he moved from his technical role to a more tactical role, taking on the newly created position of external relationships manager. He is responsible for securing government funding to carry out the company’s R&D work in Australia, Canada, New Zealand, and the United States. He also helps establish collaborations with academic research groups to work on emerging technologies that could be used to create new products.
Singh enjoys the broader scope and added responsibility of his current job. “I’m now involved with deciding the kinds of vehicles to work on, technologies and components to design and test, and timelines,” the IEEE Fellow says.
Transitioning to hybrid and all-electric machinery
Earlier in his career, Singh helped Deere begin the transition away from diesel engines. As staff engineer from 2007 through 2011, he led, managed, and contributed to the design, development, and deployment of electrification technologies. Inverter technology that he developed has been used in John Deere’s 644K and 944K wheel loaders since 2012. Inverters allow a machine’s power train to run power between the electrical machines, acting like a generator or motor, and they convert electricity from AC to DC and back again.
Wheel loaders have front and back booms and buckets that move soil, sand, rocks, and other materials. The 944K weighs more than 56 tonnes, and has a bucket capacity of up to 7.65 cubic meters.
Watch this video of a 944K in action.
John Deere 944K Hybrid Wheel Loader 360° Experience www.youtube.com
During Singh’s time as a postdoctoral fellow at the École de Technologie Supérieure, at the University of Quebec, in Montreal, his research involved an indirect-current control technique to reduce harmonics created when different AC waveforms (voltages and frequencies) would create component-damaging heat; the system he developed kept the voltage free of harmonic distortion. Singh’s work is generally being used in non-Deere applications, such as a battery-charging system connected to distributed energy resources like solar, wind, and diesel generators.
The benefits of electric industrial vehicles
Moving from diesel to hybrid and all-electric industrial vehicles offers many benefits, Singh says. For the operator, the machines are significantly less noisy and easier to control. For the owner, the vehicles reduce costs because they have greater fuel efficiency and less tire wear, and they require fewer repairs. They also emit less greenhouse gasses, which is both a company goal and increasingly mandated by governments.
Like the automotive industry’s move to hybrid and all-electric vehicles, the industrial-machine transition requires new designs, software, and materials to be developed and tested. That was Singh’s job when he joined the company’s advanced power-electronics department in 2011 as a senior staff engineer. He worked on high-efficiency electronics systems, including wide-bandgap power-conversion technologies for EV inverters.
Semiconductor devices made with wide-bandgap materials such as silicon carbide (SiC) and gallium nitride (GaN) can operate at much higher voltages, temperatures, and frequencies than traditional silicon devices can. These materials allow components like inverters to be smaller and more energy efficient, Singh says.
“Power electrics and electrification of agricultural equipment can help change our world for the better by reducing the equipment’s greenhouse gas footprint, and providing food and fiber to feed, house, and clothe the world.”
To accelerate Deere’s electrification evolution, from 2015 through 2021, Singh and his group collaborated with researchers from the U.S. Department of Energy’s National Renewable Energy Laboratory to develop a 200-kilowatt, 1,050-volt silicon carbide inverter, which is now used in the 644K and the 944K. The collaboration with NREL led the company to receive funding through a U.S. government program to reduce greenhouse gas emissions.
Singh says his current job of securing government funding and establishing relationships with university groups is necessary in research areas where the company lacks the expertise, time, and resources.
“Government funding helps the company pursue research and innovation significantly sooner,” he says. “Without it, we might have to postpone our efforts another 5 to 10 years. With it, innovation is accelerated in developing and adopting new technologies.”
Singh is still involved in developing new technologies as he continues to explore emerging tech and its application to farming and construction equipment as a John Deere Fellow.
Becoming a power electronics expert
Singh was the first in his family to go to college. He earned a bachelor’s degree in electrical engineering in 1989 from Mohan Malaviya Engineering College in Gorakhpur, India. (This institution became the Madan Mohan Malaviya University of Technology in 2013). He went on to earn a master’s degree in engineering in 1991 from the Indian Institute of Technology Roorkee, in Uttarakhand, and a Ph.D. in engineering in 1996 from the Indian Institute of Technology Delhi.
This was followed by postdoc positions working on various aspects of power electronics, including power-quality control, and AC-to-DC and DC-to-DC converters for use in telecommunications products. Singh spent about two years as a postdoc at ETS Montreal and then a year as a research fellow at Concordia University, also in Montreal.
In 2000, he became an assistant professor of electrical engineering and computer science at Tulane University, in New Orleans. There he was involved in R&D projects on power quality control converters and renewable energy systems. He taught courses in power electronics, microelectromechanical systems, and RF engineering.
Advice for future power engineers
There are many career opportunities for engineers who want to work on power electronics, Singh says. That includes working on solar and wind power, electric vehicles, industrial power, and consumer electronics.
If you’re interested in learning about how to convert gasoline-powered vehicles to electric ones, Singh suggests taking at least one course in power systems to understand how EV power systems work. Also consider taking a power-electronics course and learning about power topologies, which are the various ways that power components may be interconnected, he says. To design semiconductor devices that use new materials like SiC and GaN, learn some materials science.
Does Singh get to test-drive the vehicles he’s helping electrify? The answer is yes.
“It’s incredibly rewarding to test-drive a machine that I’ve helped to develop,” he says. “It’s one thing to talk about how it will benefit customers, but it’s a whole other thing to experience the machine the way our construction workers get to. It’s one of the best aspects of my job.”
Reference: https://ift.tt/agNe48U
No comments:
Post a Comment